
The fast growing developments in machinery industry have led to the need for designing light-weight and more reliable components. Because of its compact structure, high transmission precision and strong load bearing capacity, gear transmission is widely used in vehicles, machine tools, railways, aerospace and other mechanical systems. Gears are the most important components in machinery for transferring power and motion. The prediction of crack propagation path shows the tooth fracture in our case study and is consistent with the experimental results in the literature. The variation of meshing load results in longer fatigue life prediction compared to conventional non-coupling analysis. The load carried by the cracked tooth during the double-tooth engagement is found to decrease with crack growth. The existence of tooth root crack causes the reduction of meshing stiffness and the variation of contact load on cracked tooth. The time-varying moving load obtained from meshing analysis was then applied as the boundary condition of crack propagation.
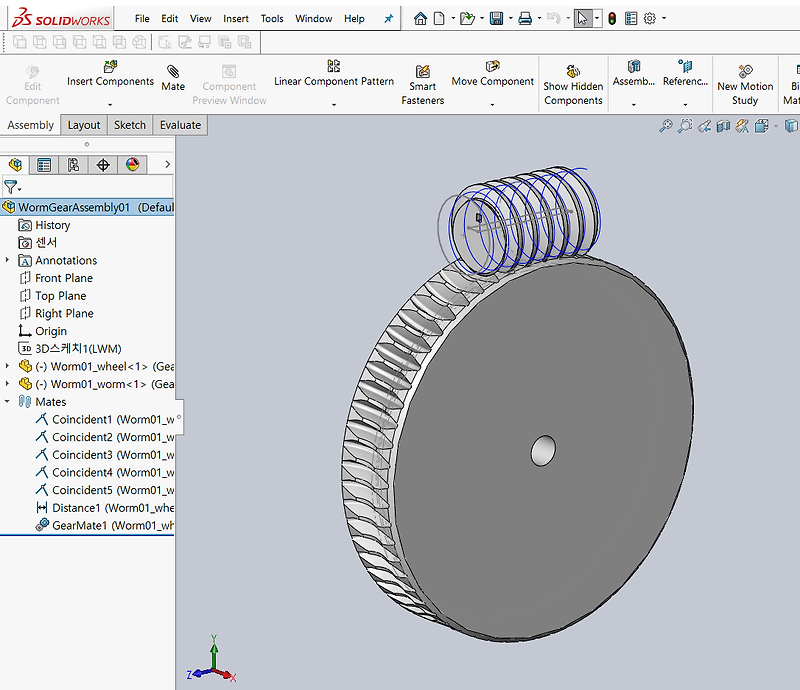
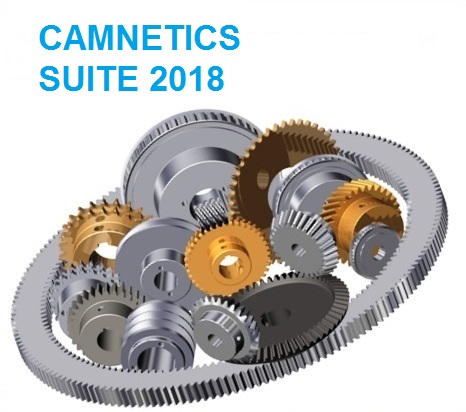
The crack morphology in the meshing analysis was updated by extracting the signed distance function value from crack propagation analysis. A standard and an extended finite element model were developed for gear pair meshing and crack propagation, respectively. This paper presents a study of the coupling behavior of spur gear meshing and tooth root crack propagation. Fatigue and fracture behavior at tooth root during gear meshing are critical to the gear transmission performance.
